Managing Propane Supply Chain Challenges
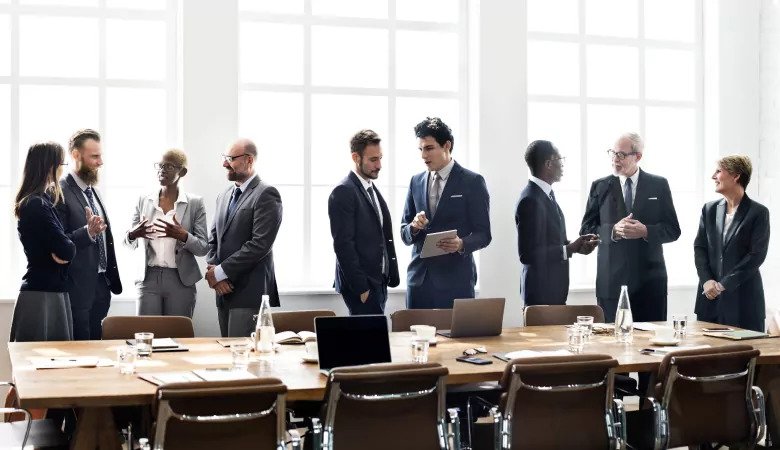
The propane industry has seen its resilience tested amidst supply chain disruptions. These interruptions, caused by factors ranging from geopolitical issues to natural disasters, pose a significant challenge. Here, we explore strategies propane businesses can implement to manage and adapt to these disruptions, ensuring reliability in service and maintaining customer trust.
Understanding the Vulnerabilities
The first step in proactive management is recognizing the weak links. The propane supply chain spans production, storage, transportation, and delivery. Disruptions can occur at any stage and stem from:
1. Production Shortfalls: Unexpected shutdowns of refineries or manufacturing plants can lead to supply shortfalls.
2. Transportation Hiccups: Dependence on pipeline networks, trucks, and railways means that transportation issues, whether due to logistical errors, strikes, or shortages in commercial drivers, can cause significant delays.
3. Storage Constraints: Inadequate storage capacity during peak usage times can strain the supply, unable to buffer the gap during sudden demand spikes.
4. Regulatory Impediments: Changes in energy policies or environmental regulations can impact supply chain efficiency and costs.
5. Natural Disasters: Hurricanes, floods, tornadoes, or extreme winter weather can severely disrupt production and delivery.
Strategies for Proactive Management and Adaptation
To fortify against these potential disruptions, propane companies need a combination of strategic planning measures, investment in infrastructure, and agile response mechanisms. A business focused on those areas will be sure to implement the following strategies:
1. Diversification of Suppliers: Relying on a single source for propane is a risk. Engaging multiple suppliers, possibly from different geographical areas, can mitigate the effect of regional disruptions.
2. Investment in Infrastructure: Enhancing storage facilities can provide a larger buffer during supply disruptions. Similarly, investing in a diverse set of transportation modes – like a company-owned fleet of trucks – reduces dependency on third-party services.
3. Advanced Demand Forecasting: Utilizing advanced analytics to forecast demand more accurately can help companies prepare better for market fluctuations. This preparation involves adjusting procurement, storage, and distribution plans accordingly.
4. Flexible Contracting: Building flexibility into contracts with suppliers can ensure more reliability in times of crisis. These contracts can include agreements on supply priority during shortages or alternative supply arrangements.
5. Technology Integration: Implementing technology like IoT for real-time tracking of shipments and inventory levels can provide early warnings of potential disruptions, allowing for timely countermeasures.
6. Regulatory Preparedness: Keeping abreast of regulatory changes and actively engaging in industry and governmental dialogues ensures that companies are not caught off guard by new rules. It also allows them to influence policy decisions constructively.
7. Customer Communication Protocols: Establishing transparent communication with customers during disruption helps businesses manage expectations and maintain trust. Proactive outreach with real-time updates about how the company operates reflects a customer-centric approach.
8. Business Continuity Planning: A detailed business continuity plan (BCP) that addresses various supply chain disruption scenarios prepares companies to act swiftly and efficiently. Regularly updated BCPs, informed by recent incidents and near-misses, keep the strategies relevant.
Long-Term Benefits
Tackling supply chain disruptions in the propane industry requires a multifaceted risk management strategy, operational flexibility, and constant communication. By investing in robust infrastructure, technology, and strategic planning, companies can mitigate the impacts of unforeseen events. Proactive and adaptive management safeguards business operations and reinforces customer confidence in the company’s reliability, ultimately contributing to a more substantial brand reputation